Cette publication est également disponible en :
Français
Once a perfumer’s creation has received approval from the brand, how does it go from there to becoming a mass-produced fragrance? What stages are involved in the weighing out process? At what point does quality control take place? Cristina Castellanos, head of operations at Iberchem in Murcia, in southeast Spain, tells us how the production process unfolds at this Spanish composition company specialising in fine and functional fragrances.
Before the production process begins, what sorts of checks do you carry out on the raw materials?
The ingredients undergo a series of tests when they arrive at the factory. We carry out a sensory evaluation to check their olfactory qualities before measuring their physical properties, like density or refractive index, which have to meet specific standards. We then analyse them using a chromatograph to check the purity of their composition, particularly the presence of molecules such as allergens, which are not allowed to exceed a certain predefined level. The next stage is storage, which is vital for ensuring that the raw materials retain their properties. Citrus fruits, for example, are kept in cold stores.
What challenges are posed by the large-scale production of a perfume?
Producing concentrate is a relatively simple process, carried out at room temperature and atmospheric pressure. The main difficulty lies in the quantity and diversity of raw materials used in a formula. You have to handle and blend a multitude of natural and synthetic ingredients. Some of them are liquid, like neroli essential oil, while others are solid, such as vanillin and coumarin, which takes the form of crystals, and others again are viscous, like synthetic sandalwood molecules, for example. During the production process, all the ingredients are treated in liquid form: the ones that are already liquid are incorporated at room temperature, the others are heated up.
Which safety and quality norms apply during the weighing out process?
We use a great number of products so it’s important to avoid contamination: we are required to ensure that the concentrate contains no traces of any compounds that shouldn’t be there. To meet this requirement, we use a system of independent pipes to carry most of the raw materials to the robot that does the weighing out. As for the ingredients we don’t use often enough to warrant a specific pipe, they are weighed out by hand with single-use tools, scoops or pipettes. We also pay very close attention to cleaning the facilities as a further measure to avoid contamination. We use containers made of stainless steel, which is inert. Once production has finished, the tanks where the concentrate has been stored are thoroughly cleaned using hot water and odourless detergent, then dried using compressed air.
Traceability is another crucial part of the production process. Each raw material is identified with a barcode which is scanned when it is used. If a mistake arises with an ingredient or quantity, the computer system automatically stops production. Once weighing out has finished, a final report details the materials’ batch number, production date, and expiry date so that all the information is on hand in the event of a problem.
How do you manage to stay true to the perfumer’s original creation?At the end of the production process, the concentrate undergoes several sensory and chromatographic analyses to check that its quality and quantity conform. The final stage involves the perfumer assessing the concentrate: they smell it to check it hasn’t deviated from the original formula and compares it to a standard sample weighed out in the laboratory.
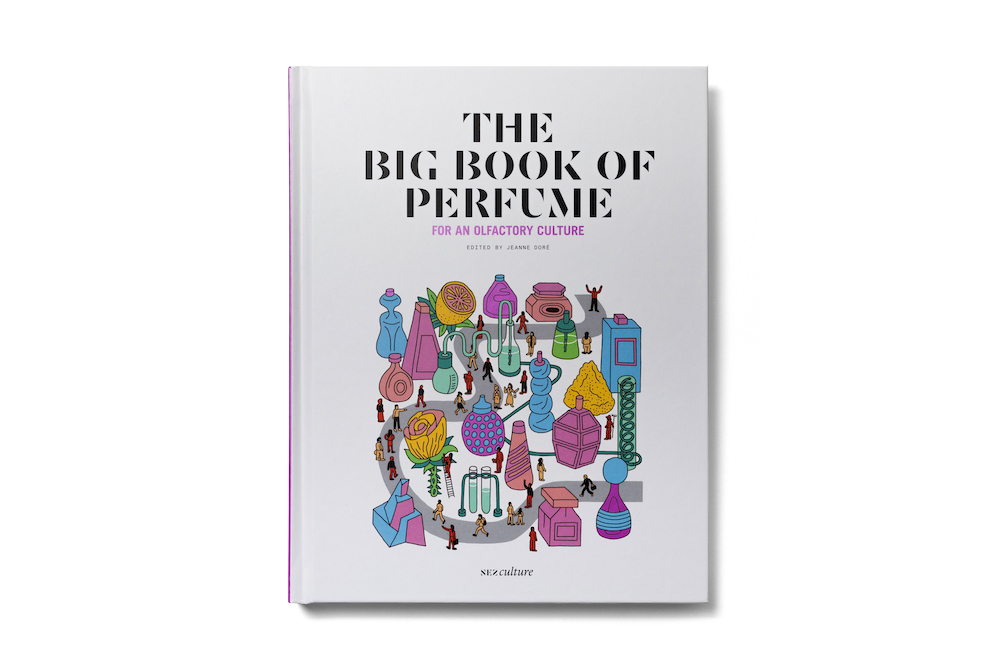
This interview is from : The Big Book of Perfume, Collective, Nez éditions, 2020, 40€/$45
- Available for France and international: Shop Nez
- Available for North America: www.nez-editions.us
Comments